Aug 18, 2011
Gleason – The Total Gear Solutions Provider
At EMO 2011 in Hannover, Gleason Corporation will present the most comprehensive line of gear manufacturing solutions in the world. In a 700 square meter booth Gleason leads the way in innovative solutions for gear manufacturing, including three new machine products being introduced for the first time. In addition, the company will be exhibiting the latest product and process technologies and developments, combining the know-how and experience in gear production technology that customers have come to expect from Gleason. This experience is reflected in a variety of soft and hard manufacturing processes for both bevel and cylindrical gear production and inspection. Our solutions are rounded out with a full line of gear cutting tools, workholding equipment, services, software and training, providing customers with a full high-performance set of solutions to suit your specific requirements.
Gleason Corporation's mission is to be The Total Gear Solutions Provider™ to its global customer base. Gleason is a world leader in the development, manufacture and sale of gear production machinery and related equipment. The Company's products are used by customers in automotive, truck, aircraft, agriculture, mining, windpower, construction, power tool and marine industries and by a diverse set of customers serving various industrial equipment markets. Gleason has manufacturing operations in Rochester, New York; Rockford, Illinois; Dayton, Ohio; Munich and Ludwigsburg, Germany; Studen, Switzerland; Bangalore; India, and Suzhou, China and has sales and service offices throughout North and South America, Europe and in the Asia-Pacific region.
More information about Gleason Corporation is available on the World Wide Web at http://www.gleason.com.
Introducing: Gleason Titan® 1200H Hobbing Machine - Gear hobbing without compromises.
The Gleason Titan® 1200H Hobbing Machine sets new standards for gear hobbing with respect to productivity, ease of operation and overall performance.
Special features:
√ Machine design for optimum chip disposal during dry and wet cutting, and ergonomically optimized accessibility.
√ Composite steel machine bed provides maximum damping characteristics, which in conjunction with the new patent-pending guiding principle, presents a quantum leap forward in overall system stiffness.
√ New operator interface and software is based on a Siemens 840D SolutionLine control system for maximum ease of use.
√ Energy efficiency advantages, thanks to the latest drive and motor technology and software capabilities to closely monitor and manage power consumption.
√ Capable of the productivity, flexibility and consistent quality that have made Gleason the leader in this market. Gleason Titan® 1200H – the new benchmark.
Introducing: Gleason Genesis® 400H Hobbing Machine
The Genesis® 400H Hobbing Machine is a new addition to our line of hobbing machines that combines proven features of the past with the latest design technologies to take productivity to a new level.
Special features:
√ Ergonomically optimized workholding and tool change, and flexible automation for faster changeover and high productivity.
√ Compact footprint with slim profile; ideal for use in cells and to reduce operator or automation movements.
√ Service and chip evacuation at the rear of the machine; provides greater freedom of automation options and possibilities.
√ Maximum flexibility through the modular concept of the machine. This especially applies to the possibility of choosing between two direct-drive workspindles, three different high-performance hob heads and the use of different tool interfaces.
√ Whether small batch production or mass production, the Gleason Genesis® 400H Hobbing Machine is the optimum solution for gear hobbing.
Bevel Gear Cutting Machine Phoenix® 280C
Up to 35% increase in productivity at maximum quality level.
Bevel gear manufacturers expect modern gear-cutting machines and processes to be capable of producing bevel gears to the required precision with considerably increased productivity. The Phoenix® 280C from Gleason does both, representing a significant step forward in gear-cutting technology.
√ Productivity: A substantial increase in productivity by integrating the part loading system, allowing gears and pinions to be changed in as little as 5 to 7 seconds. Processes such as deburring and spinning-off in wet machining are performed during the primary production cycle to eliminate non-productive time.
√ Chamfering and Deburring: This process is carried out on the optional loading station. Both heel and toe can be chamfered and deburred entirely within the primary production cycle time.
√ Quick change tooling: Particular attention has been paid to changeover time which has been minimized using quick-change equipment for cutting tools, workholding and part loader tools. The Phoenix® 280C offers the same excellent ergonomic characteristics as its predecessor.
√ Machine features: While the 280C retains the extremely rigid monolithic column design of previous Phoenix machines, there is a new approach to the frame, which is cast from an advanced polymer composite material, providing significant improvements in thermal stability and damping in particular. Chip evacuation has also been optimized, preventing cutting chip build-up in the work chamber. The 280C is the perfect machine for dry cutting of bevel gears.
√ Software: The Phoenix® 280C has an innovative user interface suitable for both Fanuc and Siemens control systems. Machine operation is very simple and intuitive, and the machine may be operated after only a brief operator introduction. The operating instructions and videos can be called up to support any troubleshooting required.
√ Integrated measurement: The on-machine measurement system will measure tooth flank form and pitch, and the measured results compared with customer-supplied part data. If the part is within the tolerance, the machine can continue to run parts while the part goes through the customer inspection room.
Introducing: Analytical Gear Inspection System 2000GMS
Gleason Metrology Systems introduces the 2000GMS, the latest model in the growing line of GMS series Analytical Gear Inspection Systems. The 2000GMS will be fully operational at EMO and will measure a test workpiece of approximately 1500 mm diameter. The 2000GMS is the first of three five-axis machines developed for the large power transmission gearbox market sector, which includes wind energy applications. GMS models offer a host of new features and technology improvements.
Highlights:
√ IP54 rated, CE 2009 certified electrical cabinet designed for today's factory environments.
√ GAMA 2.0 (Gleason Automated Measurement and Analysis) object oriented (native Windows®) suite of Gear, Gear Tools and Rotor measurement software.
√ Reduced cycle times, GAMA 2.0 offers up to a 45% cycle time reduction over previous GAMA versions (gear style dependent).
√ Multiple language support, all software modules can operate in multiple languages or can simply print the resultant output charts in any of a host of the world's languages (all major languages supported)
√ New ROP (remote operator pendant) which allows the operator to maneuver the machine conveniently from the measurement zone of the workpiece, Operators can invoke certain measurement and set up commands, adjust speeds and feeds, as well as "teach" measurement positions.
√ The new ROP is also a complete telephony device when the machine is connected to the internet. Standard features
- internal microphone allows VOIP communications for remote support
- "operator voice mail" – about current part / machine conditions, set up changes, and any other pertinent process updates.
- web cam for remote diagnostics, supports standard work instruction creation, photograph the workpiece set up.
√ All GMS models support APC (automatic probe changer) functionality and incorporate the Renishaw® SP80H digital 3D scanning probe head for the inspection of today's most complicated gear shapes and support prismatic part measurements for non-gear features.
Agilus® 180TH Multi-functional Machine
Turning – drilling – hobbing – chamfering and deburring - in a single setup!
The Agilus 180TH features a universal and highly productive multi-functional concept capable of machining shaft and disk-shaped workpieces in a single setup (one-piece flow).
This machine provides state-of-the-art technology and machining processes for all types of cylindrical gears which can be produced by hobbing.
The tool turret for locating fixed or driven tools allows turning, drilling and milling operations as well as hobbing and subsequent generating chamfering and deburring to be performed in the same setting.
The CNC-controlled tailstock enables the machine to clamp a broad range of workpieces with support on both sides to guarantee optimum rigidity during machining.
Gleason's Quick-Flex® workholding concept, the quick-clamp option for the cutting tool and optimal accessibility satisfy requirements for rapid, user-friendly workpiece change.
The Agilus 180TH can be operated in a fully automatic mode in conjunction with one or more turning cells. This innovative concept allows complete manufacturing tasks to be performed on a small, compact footprint.
Cutting Tools
All gear-cutting tools from a single source.
Gleason supplies virtually every type of cutting tool for the production of cylindrical and bevel gears. Enjoy the benefits that Gleason can offer you as a supplier of the complete range of gear-cutting technologies. Our cutting tool specialists are familiar with the requirements of the process chains in modern gear production, enabling us to optimize your full range of cutting tools required from start to finish.
Our range of products for bevel gear cutting includes tools for cutting and grinding straight, spiral and hypoid bevel gears. For cylindrical gear cutting, we offer hobs, form relieved milling cutters, shaper cutters, chamfering and deburring tools, shaving cutters, honing tools, coated diamond and CBN grinding wheels, diamond dressing wheels and diamond dressing rolls.
OPTI-CUT® gear-cutting tools
Why not benefit from the productivity advantages offered by this advanced replaceable indexable carbide insert technology? The OPTI-CUT® product line includes tools for gear gashing, hobbing and shaping in a range of sizes to meet all requirements. Available roughing or finishing, internal or external gears, and a wide range of modules and tooth profiles.
Workholding Solutions
Workholding expertise combined with gear-cutting competence.
Who is more familiar than Gleason with gear-cutting industry requirements for holding and clamping workpieces? Gleason designs and manufactures a complete series of workholding solutions for bevel and cylindrical gears, for use on Gleason and other gear equipment.
Examples from our extensive product range:
√ Changeover times are reduced by up to 70 % by Gleason X-Pandisk® fixture systems, which automatically align workpieces weighing up to 2,000 kg, providing for a consistent machining process.
√ For large components, we also supply pallet-based set-up table systems which allow set-up to be performed in parallel with primary production. Your machine continues to produce while a new workpiece is being prepared.
√ Our Quik-Flex® and quick-change workholding designs offer significantly reduced fixture change-over times in the production of bevel and cylindrical gears up to a diameter of 200 mm. The basic modules stay in the machine permanently while intelligent quick-change systems ensure a changeover with perfect concentricity and no need for further alignment.
√ On measuring machines, our Gleason-LeCount® expanding arbors are a leading solution. They are easy to handle, allowing extremely quick clamping of any parts with bores for measurement of gears.
Also available for production applications.
Gleason Global Services (GGS) has been created to maximize your uptime.
You can rely on our more than 250 factory trained professionals serving over 30 countries throughout the Americas, Europe, and Asia, around the clock to support your needs. Who better than GGS to keep you in production with a complete range of flexible services and support.
√ Services: Full range of service programs, including preventive maintenance, machine relocations and reinstallation, machine inspection/troubleshooting/repair, recertification.
√ Service parts: Rapid deployment from 8 global stock locations.
√ Training: Industry's largest array of training programs available to support customers globally.
√ Service programs: Available in a variety of customized levels.
√ Application development: Solutions to optimize processes.
√ Equipment upgrades: Comprehensive solutions to enhance productivity and lower your total cost of ownership.
√ Remote services: Designed for rapid response, anywhere, anytime.
√ 24 hours a day, 7 days per week: After-hours coverage to keep Gleason machines up and running.
Technical support for the Total Solution
Reduced development cycles for new technologies are putting gear producers under increased pressure to innovate and remain competitive; consequently, they are forever facing new challenges, making the appropriate application of new technologies a key factor in any company's success. Highly-qualified Gleason engineers and application specialists offer every customer the perfect solution to suit individual requirements. Intensive close collaboration with our customers guarantees that the process technologies consistently continue to develop cutting-edge solutions.
As "The Total Gear Solutions Provider", we are ready and prepared to address ever-changing customer requirements, and we consider technical consulting an important component of our corporate strategy and of our value to the customer.
Gleason provides its customers with:
√ Gear design software
√ Technical consulting
√ Process optimization to include machines, tools and workholding equipment
√ Tool designs
√ Prototyping and development support for new jobs on our machines for specific technologies
√ On-site support.
For further information at EMO Hanover, please contact Messrs. Günter Schmidt or Udo Stolz at Booth G04 in Hall 26.
Before, during and after the exhibition, information can be obtained from:
Gleason Sales (Germany), Daimlerstrasse 14, D-71636 Ludwigsburg, Germany, Tel.: +49-(0)7141-404-455 (Mr. Schmidt), Fax: +49-(0)7141-404-500, e-mail: gschmidt@gleason.com or our website www.gleason.com.
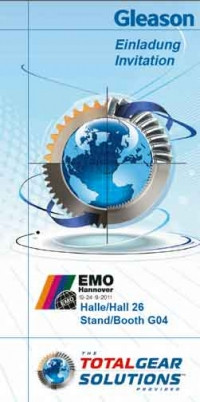