22º jan. 2010
Gleason’s new AGILUS® 180TH Multi-Functional Machine performs turning, drilling, milling, hobbing and chamfering/deburring operations in a single setup for all types of shaft- and disc-type cylindrical gears up to 180 mm in diameter, with shaft lengths up to 500 mm, delivering a host of significant benefits over conventional multi-machine processes.
Contemporary gear production is characterized by reduced batch sizes, increased accuracy requirements and increased complexity of workpieces.
As compared to typical production of cylindrical gears requiring hobbing, the AGILUS 180TH greatly reduces the number of machines, setups and overall through-put times for the complete processing of the gear, thus reducing both the capital investment and cost per workpiece for the user. AGILUS’ ability to perform, in a single setup, complete machining of a wide range of shaft- and disc-type cylindrical gears also gives the user a greater degree of flexibility, higher machine availability, and optimized throughput as compared to the typical process where multiple single-purpose machines are used, requiring time-consuming changeover from part to part.
The AGILUS machine is equipped with an innovative, high-speed tool turret for locating fixed or driven tools for the complete range of turning, drilling and milling operations as well as the workpiece loading and unloading function via active grippers on the turret. The hobbing operation is enabled by the implementation of a proven Gleason hob head. Subsequent chamfering and deburring operations can be placed on the turret as an option. Adding to the machine’s universal machining capability is the CNC-controlled tailstock, which enables Agilus to clamp a broad range of workpiece types and sizes, while at the same time providing optimum rigidity during machining to help maximize cutting feed rates.
In addition, Gleason’s Quick-Flex® workholding concept, and a quick-clamp option for cutting tools for rapid, user-friendly tool-change, combine to greatly reduce non-productive setup time, particularly as compared to when parts are processed sequentially on multiple machines.
The AGILUS 180TH is also easy to integrate into existing manufacturing environments, not only because of its compact, single-machine footprint, but also due to a universal automation interface that provides an easy, flexible connection to sliding chain belts, chain-type conveyors, workpiece stack cells, and other types of automation and storage systems.
AGILUS is designed to operate at the same high level in either wet, or completely dry cutting conditions. For optimal machining of thin shafts, workpiece clamping is performed under tensile load, providing exceptionally high hobbing quality and productivity.
Gleason Corporation’s mission is to be The Total Gear Solutions Provider™ to its global customer base. Gleason is a world leader in the development, manufacture and sale of gear production machinery and related equipment. The Company’s products are used by customers in automotive, truck, aircraft, agriculture, mining, windpower, construction, power tool and marine industries and by a diverse set of customers serving various industrial equipment markets. Gleason has manufacturing operations in Rochester, New York; Rockford, Illinois; Dayton, Ohio; Plymouth, England; Munich and Ludwigsburg, Germany; Studen, Switzerland; Bangalore, India; and Suzhou, China, and has sales and service offices throughout North and South America, Europe and in the Asia-Pacific region.
More information about Gleason Corporation is available on the World Wide Web at http://www.gleason.com.
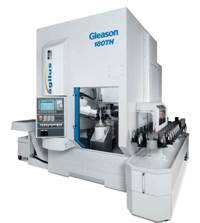