21º jan. 2013
Honing is a fast, well-proven process in the gear manufacturing industry. It is used in high-volume production environments where every second in cycle time counts.
Most honing machines are now equipped with a double flank roll tester to check parts before they are honed. Testing helps identify incorrect or damaged parts which can destroy the honing tool or parts with the wrong stock on the tooth flanks. It does not matter if the stock is too big or too small, in both cases it can lead to poor finished quality.
With the help of a double flank roll tester these parts can be identified and separated for either scrap or post-treatment. This pre-checking provides three important pieces of information:
- Are the parts free of nicks, if nicks are present how big are they?
- How big is the run out?
- What is the size of the part?
For adaptive honing two parameters must be considered, run out and the size of the parts before honing.
By using adaptive strategies for honing, the center distance between the gear and the honing stone is flexible for every single part, depending on the actual conditions. For machining time it is important to have the center distance as short as possible before starting the honing process.
Until now this initial or starting center distance was set up by calculations and theoretical values. Factors considered were the nominal stock/flank and the lowest acceptable pre-machining quality. To avoid potential problems this required a considerable safety distance between the work and the honing stone; meaning, that when the process starts the tool only “cuts” air before it contacts the flanks.
The value Xu in the machining process describes the center distance where the first contacts can happen. In the past this value was fixed for the complete batch of gears.
Adaptive honing changed this situation. By using the double flank tester, all necessary parameters are known; allowing the machine to automatically calculate the optimal Xu value which enables the proper contacts between tool and gear on an individual basis, ensuring every gear is machined with an optimized value.
If the parts are of good incoming quality the Xu can be lower and the cycle time will be shorter. For poorer quality parts or for parts with higher values for the stock, the Xu will be higher.
By using this flexible adaptive process the safety distances can be far lower and therefore the process time will be reduced. Results have shown an average time savings of 10% for machining time and a safer and more stable production environment.
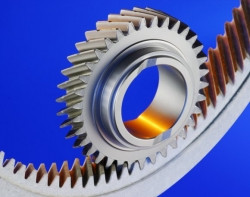